Ok, falls Ihr die erste Folge verpasst habt, hier eine kurze Zusammenfassung: Die Sneakerjagd hatte uns bis auf illegale Müllkippen in Kenia geführt, wo unsere alten Schuhe verenden und die Umwelt verschmutzen. Um etwas dagegen zu unternehmen, wollten wir einen Schuh bauen, der das Problem im Kleinen angeht. Dazu haben wir mit dem Sneakerhersteller Monaco Ducks, dem kenianischen Start-up African Collect Textiles und der Hochschule Reutlingen einen Prototypen entwickelt. Das ist seine Geschichte in fünf Bildern:
1. Sneaker-Müll aus Nairobi
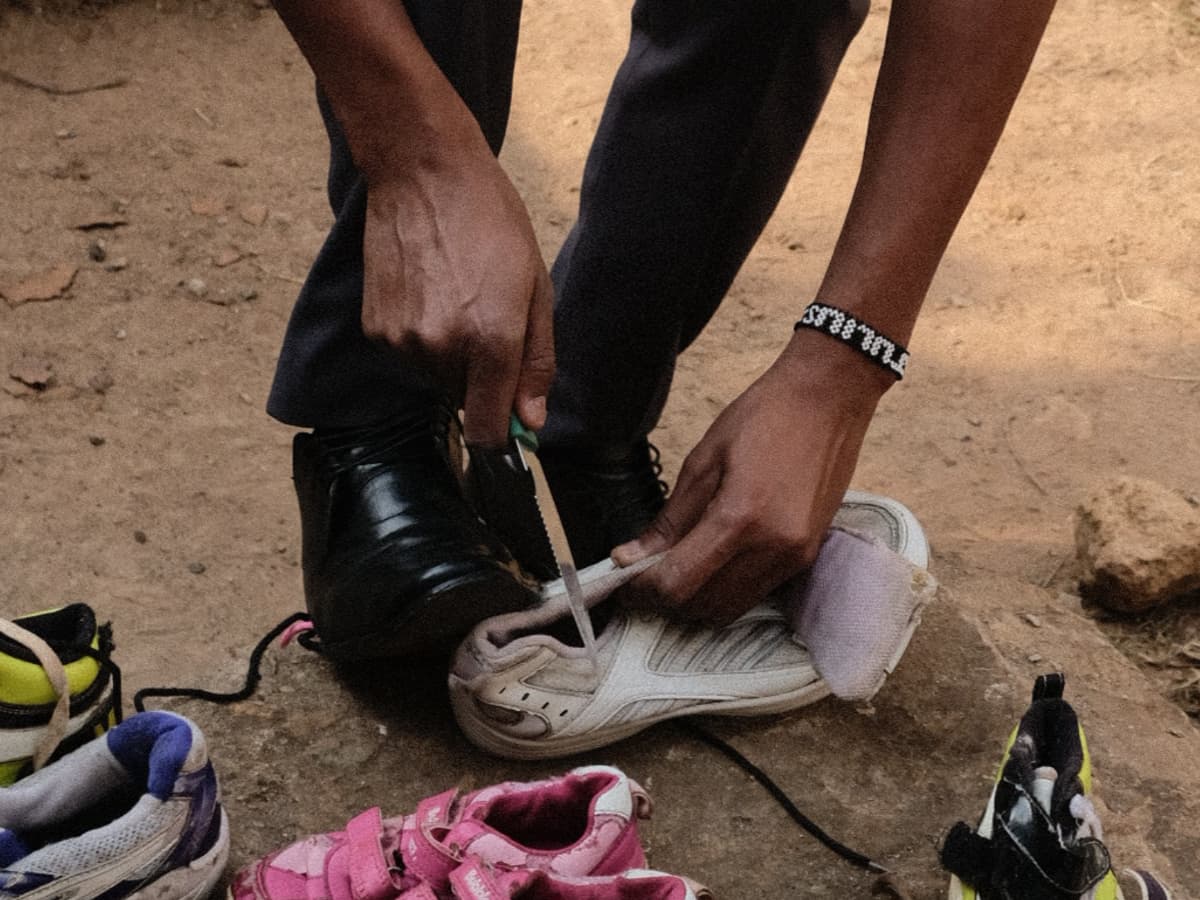
Für unseren Recycling-Sneaker brauchen wir zunächst alte Schuhe, die wir recyceln können. Naheliegend wäre natürlich, sie in Kenia von Müllkippen oder Flüssen zu sammeln, wo sie die Umwelt verschmutzen. Aber die Sneaker sind dort nur schwer einzusammeln und nur sehr aufwendig zu reinigen. Deshalb arbeiten wir mit dem Start-up Africa Collect Textiles (ACT) zusammen, das gegen den Textilmüll in Nairobi kämpft. Dafür hat es Sammelcontainer aufgestellt. Aus Kleidung, die sonst vermutlich auf dem Müll landen würde, knüpft es zum Beispiel Teppiche oder näht Taschen. Für die Schuhe hat es bislang keine Verwendung. Säckeweise stapeln sie sich in der Garage. Aus den Sohlen dieser Schuhe werden wir die ersten neuen Sohlen fertigen. Perspektivisch wollen wir die alten Schuhe aber auch woanders sammeln, kurz vor der Müllkippe sozusagen. In Episode 1 unseres Sneaker-Experiments haben wir zwei mögliche Orte vorgestellt.
2. Ab in den Schuh-Schredder
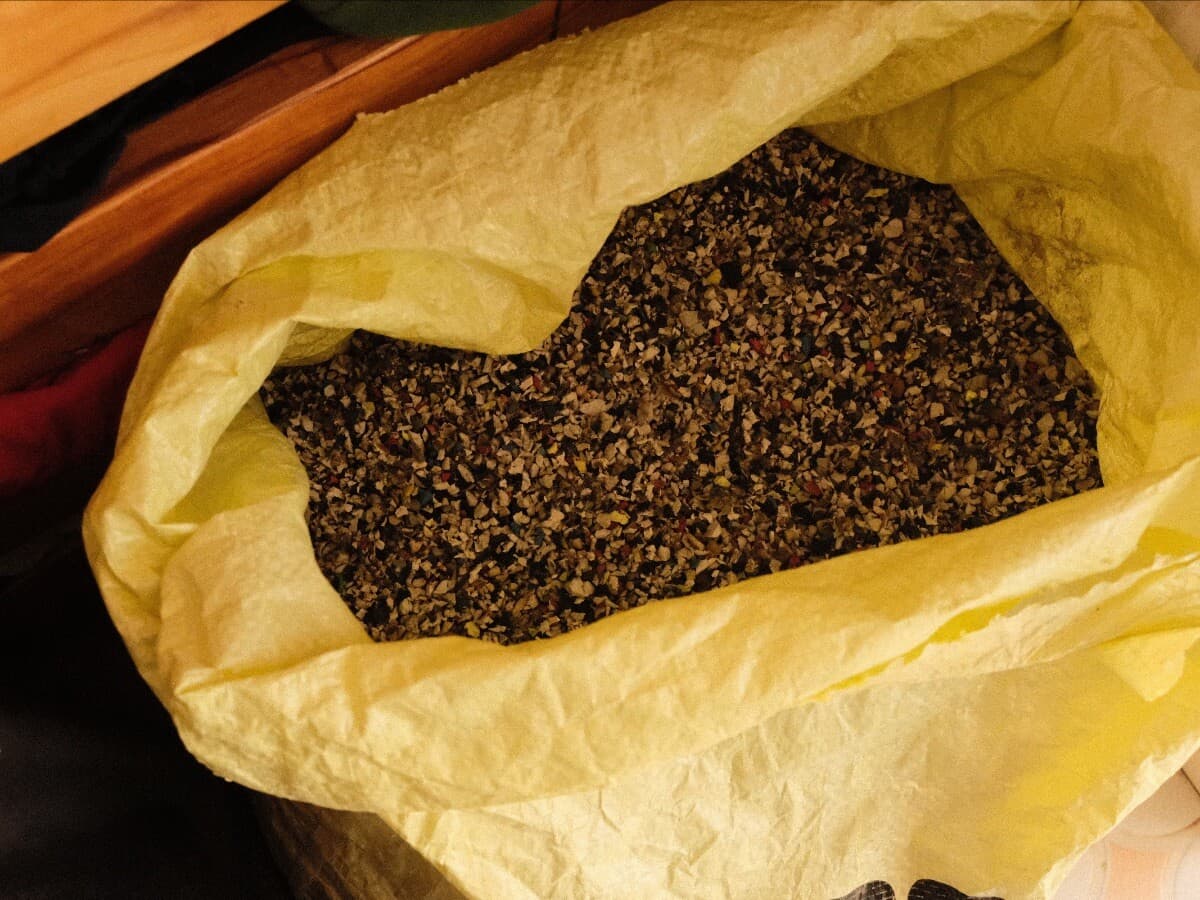
Um aus alten Schuhsohlen neue zu machen, muss man sie erst einmal zerhäckseln. Jemanden zu überzeugen, Schuh-Müll aus Afrika für einen zu zerkleinern, ist allerdings gar nicht so einfach. Letztendlich haben wir den Sohlenhersteller For Ever in Portugal gefunden. Für unseren Prototypen entsteht das Granulat dort. In Zukunft wollen wir den Schuh-Müll in Kenia schreddern. Dafür stehen wir derzeit mit dem Start-up Gjenge Makers aus Nairobi in Kontakt. Das Unternehmen verarbeitet eigentlich Plastikmüll zu Bodenplatten und Ziegelsteinen. Der Schredder, den es verwendet, um das Plastik zu zerkleinern, könnte vielleicht auch alte Schuhe zerhäckseln. Gerade bastelt Genje Makers an der Maschine herum und macht erste Testläufe.
3. Neue Sohle aus alten Schuhen
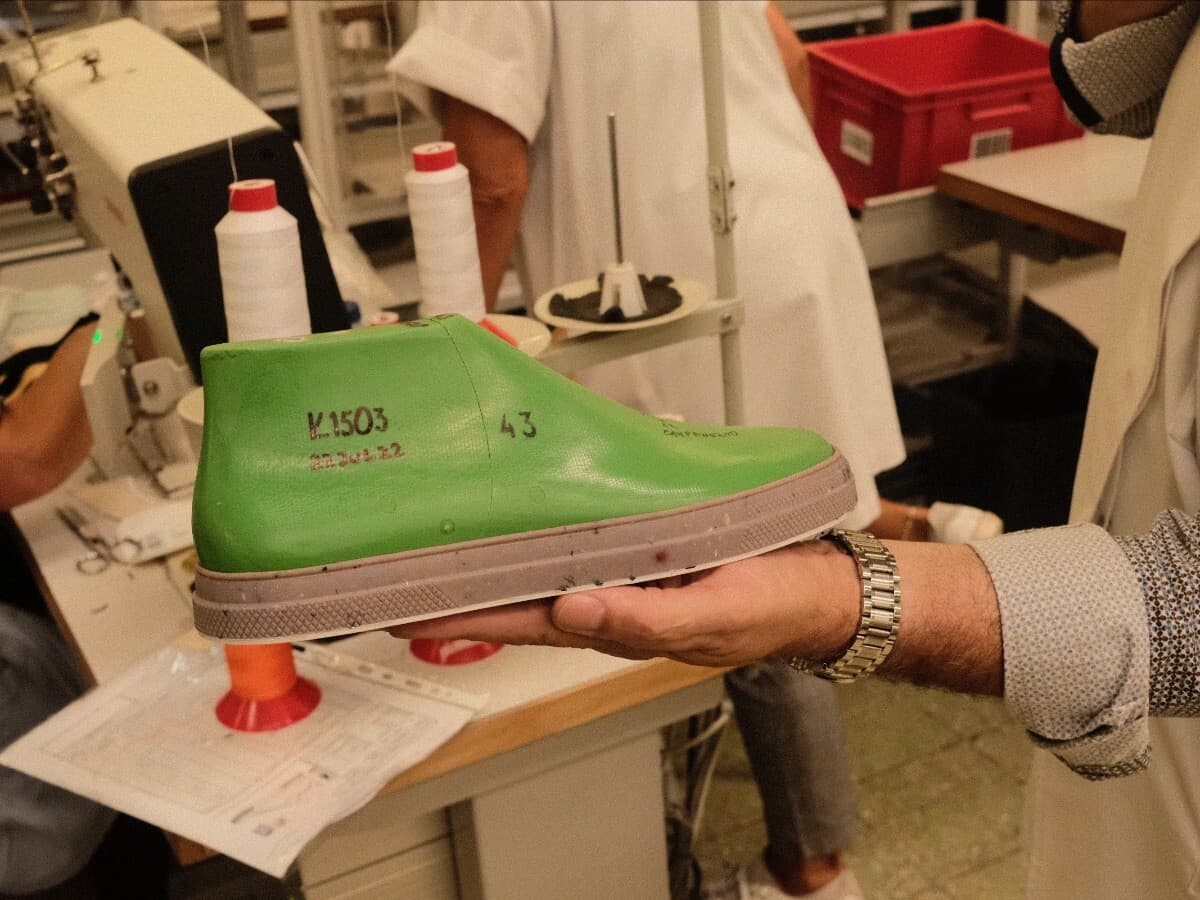
Allein aus geschreddertem Schuh-Müll lassen sich keine stabilen Sohlen herstellen. Aber wie viel Müll kriegen wir in die Sohle? Nach vielen, vielen Experimenten steht fest: Rund 25 Prozent. Mehr geht nicht, ohne dass Haltbarkeit und Qualität leiden. Klingt wenig? Nun ja, im vergangenen Jahr hatten wir ja aufgedeckt, dass Nike auch neue Schuhe schreddert, um daraus sein eigenes Grind-Material zu machen. Klar: Das ist so ziemlich das Unnachhaltigste, was man machen kann. Auch Nike aber verarbeitet das Grind dann in neuen Schuhsohlen. Zum Vergleich: In der Sohlen von Nikes “Space Hippie” stecken gerade mal 12 Prozent Grind.
Für den Rest unserer Sohle wurde extra ein möglichst umweltfreundlicher Materialmix entwickelt, der zu 90 Prozent aus nachwachsenden Rohstoffen besteht (60 Prozent Naturkautschuk, 30 Prozent Reisschalenasche). Die übrigen 10 Prozent bestehen aus Weichmachern, die in einer reineren Variante auch in der Lebensmittelindustrie zum Einsatz kommen und Zusätzen für die Vulkanisierung, einem Prozess, bei dem unter Druck und Hitze aus Naturkautschuk bewegliches Gummi wird.
Dieser Mischung wird beim Sohlenhersteller For Ever in Portugal mit dem Grind-Material gemischt und gewalzt. Dann werden einzelne Stücke rausgeschnitten und in massiven Metall-Formen zu Sohlen gepresst. Die Formen sind schon über 30 Jahre alt, weshalb die Sohlen ziemlich vintage aussehen, wenn sie aus der Presse kommen. Da wir auf keinen Fall wollen, dass das Granulat aus den alten Sneakern in Form von Mikroplastik in der Umwelt landet, haben unsere Sohlen außerdem eine extra Laufsohle, die aus dem selben Materialmix besteht wie die Sohle, nur ohne das Granulat. Sie dient als eine Art Schutzschicht.
4. Die obere Hälfte fehlt noch
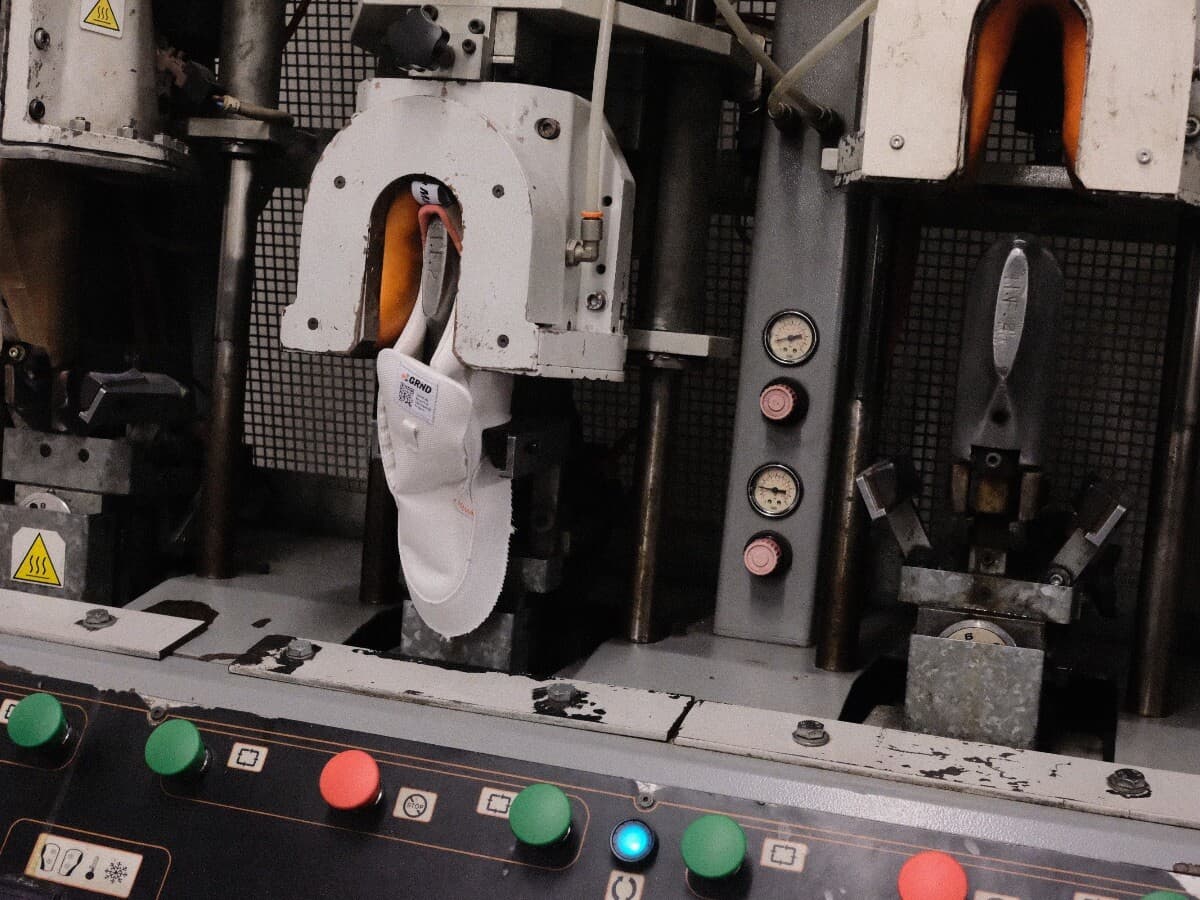
Klar: Das Besondere an unserem Sneaker ist die Sohle. Aber auch der Rest vom Schuh soll möglichst nachhaltig sein. Auch deswegen arbeiten wir bei dem Projekt mit Monaco Ducks zusammen, einem kleinen Hersteller aus München, der schon seit 2017 an einem möglichst kreislauffähigen Sneaker tüftelt.
Bei der Entwicklung waren uns drei Dinge wichtig: Erstens sollten so wenig unterschiedliche Materialien wie möglich verwendet werden, weil das ein späteres Recycling des Sneakers vereinfacht. Wir haben uns als Hauptmaterial für recyceltes Polyester entschieden, da es langlebig und recyclingfähig ist – und im Gegensatz zu neuem Polyester deutlich weniger Energie verbraucht. Zweitens sollten so viele Komponenten wie möglich aus recyceltem Material bestehen. Von den insgesamt 15 Komponenten ist das bei 13 der Fall. Und drittens wollten wir keine Abstriche bei der Qualität des Sneakers machen. Für das Nähgarn und die Polsterung haben wir deshalb auf recyceltes Material verzichtet, weil die Eigenschaften des recycelten Materials unseren Ansprüchen an Qualität und Haltbarkeit nicht genügt haben.
Ach ja, wenn aus dem Prototypen tatsächlich ein richtiges Produkt werden sollte, wird es auf die Sneaker ein Pfand geben. Mit ihm wollen wir dafür sorgen, dass die Schuhe nach ihrer Nutzung zurückgegeben und möglichst vollständig recycelt werden.
5. Genäht und gebacken
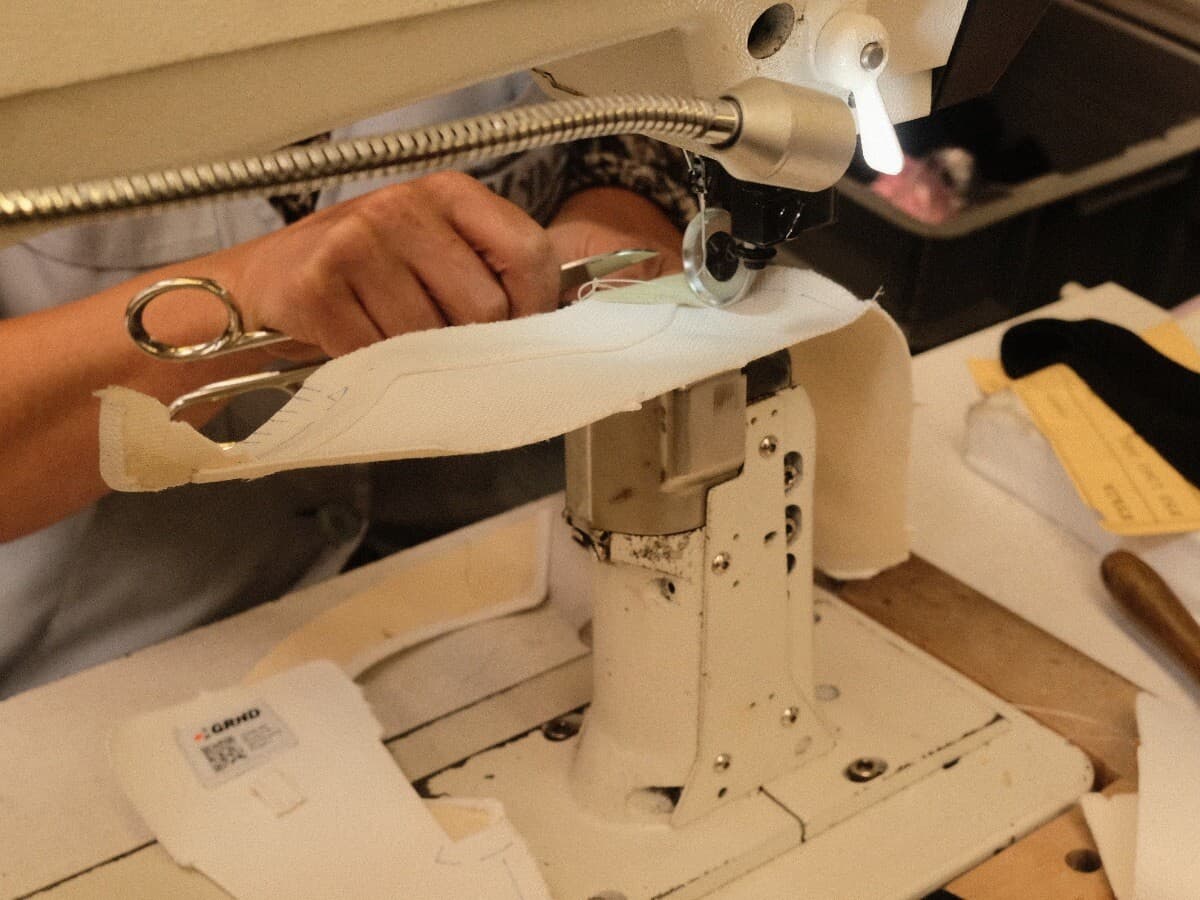
In Guimaraes, einer Bergstadt nördlich von Porto, werden unsere Schuhe schließlich zusammengesetzt. Dort sitzt das Unternehmen Kyaia, einer der größten Schuhhersteller in Portugal. Etwa 3000 Paar Schuhe stellt das Unternehmen an einem Tag her – und jetzt auch unsere Sneaker. In einem Schuh stecken rund zwei Stunden Handarbeit: Erst werden die einzelnen Teile von einem Lasercutter ausgeschnitten und mit der Nähmaschine zusammengenäht. Dann kommt der Oberschuh in den Ofen – das Material wird erhitzt und anschließend in Form gebracht. Schließlich werden Sohle und Oberschuh zusammengenäht: Fertig!
Tadaaaa!
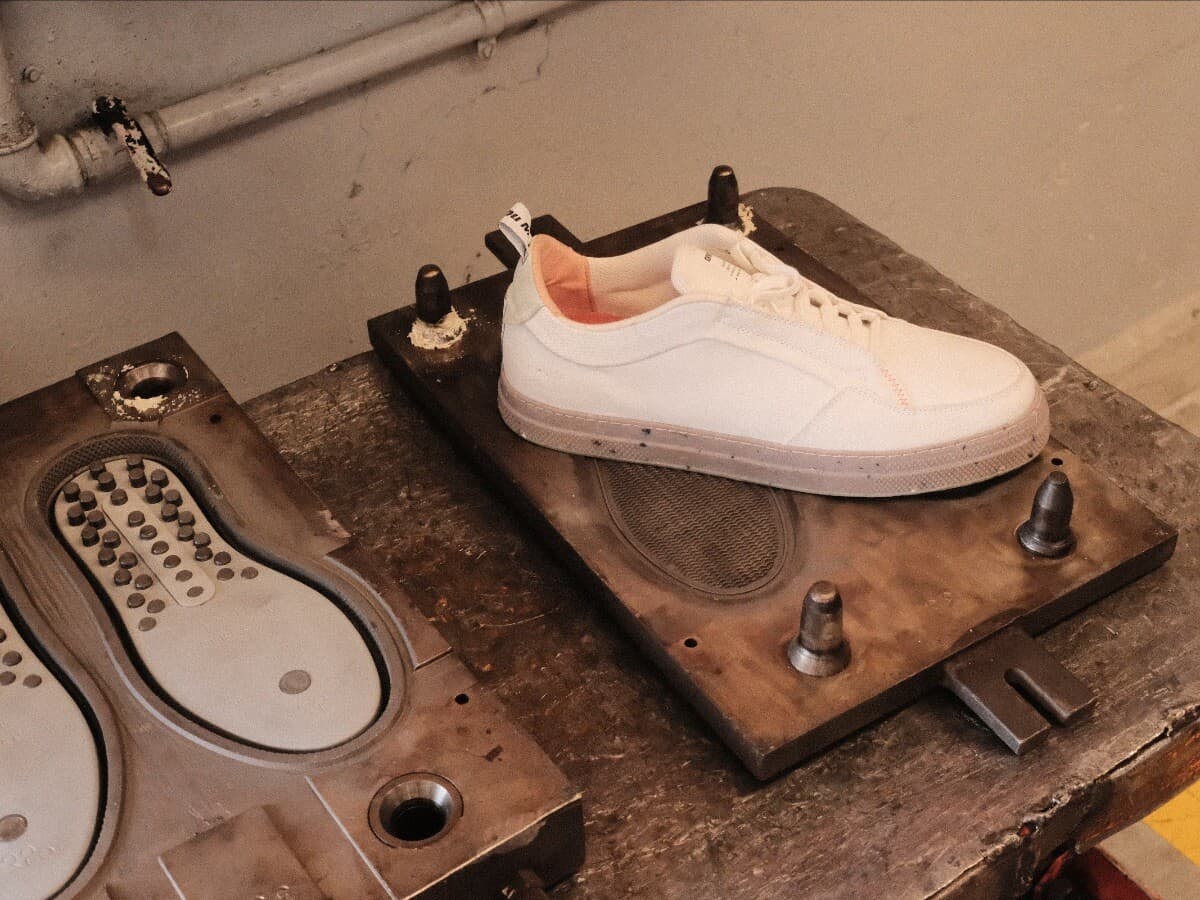
Das ist er! Wir sind stolz, ihn Euch endlich präsentieren zu dürfen. Das ist das Ergebnis unserer monatelangen Lösungssuche: Der Sneaker, der etwas gegen den Textilmüll in Kenia ausrichten soll, um den sich Nike und Co. nicht kümmern. Mit dem Abschluss des Prototypen endet unsere Berichterstattung und wir übergeben das Projekt an eine eigene Firma. Sie soll dafür sorgen, dass aus dem Prototypen eine echte Unternehmung wird.
Transparenzhinweis: In einer früheren Variante des Artikels hieß es, der Schuh enthalte Weichmacher, „die auch in der Lebensmittelindustrie zum Einsatz kommen“. Das ist nicht falsch, aber etwas unpräzise. Tatsächlich kommt der enthaltene Weichmacher in der Lebensmittelindustrie zum Einsatz, allerdings in einer reineren Variante als in dem Schuh. Es handelt sich bei dem Weichmacher um ein biobasiertes Weißöl, das aus nachwachsenden Rohstoffen wie etwa Raps oder Sonnenblumen gewonnen wird und das gesundheitlich unbedenklich ist. Wir haben die entsprechende Stelle präzisiert.
So geht's weiter
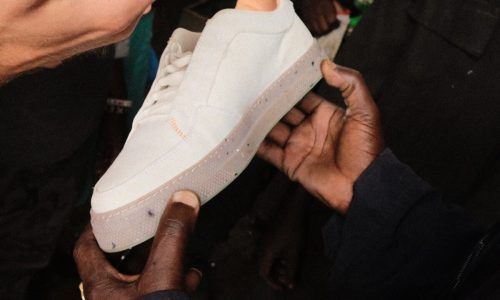
Vom Prototypen zum Crowdfunding
Das Experiment nähert sich dem Ende. Ein Prototyp konnte erfolgreich entwickelt werden, nun startet ein Crowdfunding.